硬泡催化剂 BDMA 与快速脱模工艺的结合 一、引言 聚氨酯硬泡作为一种性能优异的高分子材料,凭借其低密度、高强度、良好的保温隔热性和耐化学腐蚀性,被广泛应用于建筑保温、冷藏设备、交通运输等领域。在...
硬泡催化剂 BDMA 与快速脱模工艺的结合
一、引言
聚氨酯硬泡作为一种性能优异的高分子材料,凭借其低密度、高强度、良好的保温隔热性和耐化学腐蚀性,被广泛应用于建筑保温、冷藏设备、交通运输等领域。在聚氨酯硬泡的生产过程中,催化剂的选择与工艺优化直接影响产品质量和生产效率。随着制造业对生产节奏和成本控制的要求不断提高,快速脱模工艺逐渐成为提升聚氨酯硬泡生产效率的关键技术之一。
硬泡催化剂 BDMA(N,N – 二甲基苄胺)作为一种高效的叔胺类催化剂,在促进聚氨酯硬泡反应方面表现出独特的优势。将 BDMA 与快速脱模工艺相结合,能够在保证硬泡产品性能的前提下,显著缩短生产周期,降低生产成本,满足工业化大规模生产的需求。本文将从 BDMA 的特性、快速脱模工艺的原理、二者结合的技术优势、实际应用案例等方面进行深入探讨,为相关领域的生产实践提供参考。
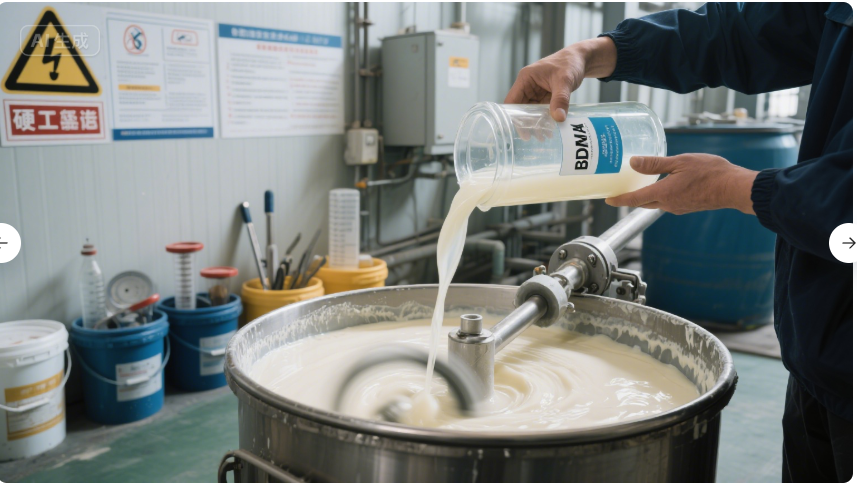
二、硬泡催化剂 BDMA 概述
2.1 化学特性与催化机理
BDMA 是一种具有芳香环结构的叔胺催化剂,其化学结构式为 C6H5CH2N (CH3) 2。从分子结构来看,苄基的存在增强了分子的空间位阻效应,而二甲胺基团则赋予其较强的碱性,这一结构特点使其在聚氨酯硬泡反应中表现出独特的催化性能。
在聚氨酯硬泡的形成过程中,主要发生两个关键反应:一是异氰酸酯与多元醇的凝胶反应(生成氨基甲酸酯键),二是异氰酸酯与水的发泡反应(生成脲键并释放二氧化碳)。BDMA 对这两种反应均有催化作用,且具有一定的选择性。研究表明,BDMA 更倾向于催化发泡反应,能够快速促进二氧化碳气体的生成,为泡沫的膨胀提供动力;同时,其对凝胶反应的催化作用可确保泡沫在膨胀过程中及时固化,避免出现坍塌或泡孔结构异常。
通过核磁共振(NMR)和红外光谱(IR)分析发现,BDMA 分子中的氮原子能够与异氰酸酯中的羰基形成氢键,降低反应活化能,从而加速反应进程。这种催化机制使得 BDMA 在较低用量下即可实现对反应速率的有效调控。
2.2 产品参数
BDMA 的物理化学参数对其在聚氨酯硬泡生产中的应用具有重要影响,以下为常见的工业级 BDMA 产品参数(表 1):
参数指标
|
数值范围
|
备注
|
外观
|
无色至淡黄色液体
|
纯度降低时颜色加深
|
密度(25℃,g/cm³)
|
0.89-0.91
|
与温度呈线性负相关
|
纯度(%)
|
≥98.0
|
气相色谱法测定
|
沸点(℃,101kPa)
|
183-185
|
随气压变化略有波动
|
闪点(闭杯,℃)
|
60-65
|
属于易燃液体,需避光储存
|
水溶性(25℃,g/100mL)
|
微溶
|
可溶于大多数有机溶剂
|
折射率(25℃)
|
1.5010-1.5030
|
反映分子结构的规整性
|
这些参数直接影响 BDMA 在聚氨酯配方中的分散性、催化活性及与其他组分的相容性。例如,较高的纯度可减少杂质对反应的干扰;适宜的沸点和闪点则便于在生产过程中控制其挥发损失,同时保障生产安全。
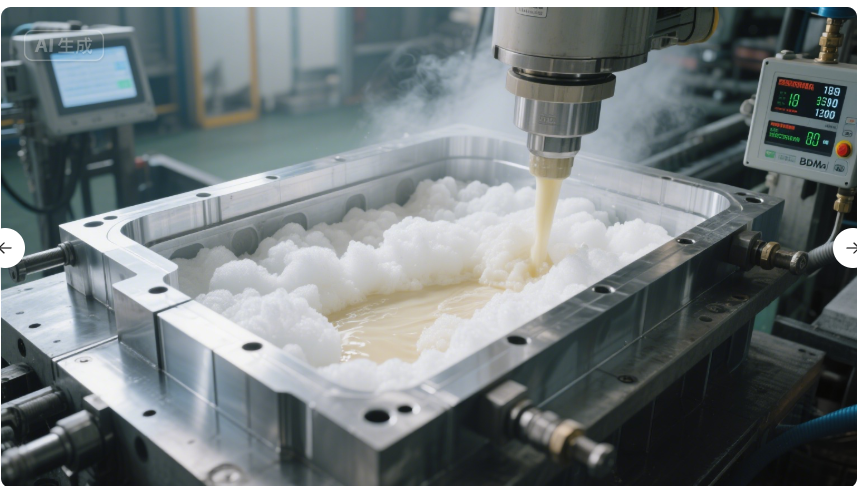
三、快速脱模工艺原理与要求
3.1 工艺核心原理
快速脱模工艺是指在聚氨酯硬泡成型过程中,通过优化反应条件和催化剂体系,缩短泡沫在模具内的固化时间,使产品能够在更短时间内达到足够的强度和硬度,从而实现提前脱模的生产技术。该工艺的核心在于 “快速固化” 与 “适时脱模” 的平衡:一方面需要加快反应速率,使泡沫在短时间内完成交联固化;另一方面需确保脱模时泡沫已具备足够的结构强度,避免出现变形、破损等缺陷。
从动力学角度来看,快速脱模工艺通过提高反应温度(模具温度、物料温度)、优化催化剂配比等方式,加快了聚氨酯反应的速率常数,使反应在更短时间内达到凝胶点和固化点。例如,传统工艺中泡沫在模具内的停留时间可能需要 5-10 分钟,而快速脱模工艺可将这一时间缩短至 2-3 分钟,甚至更短。
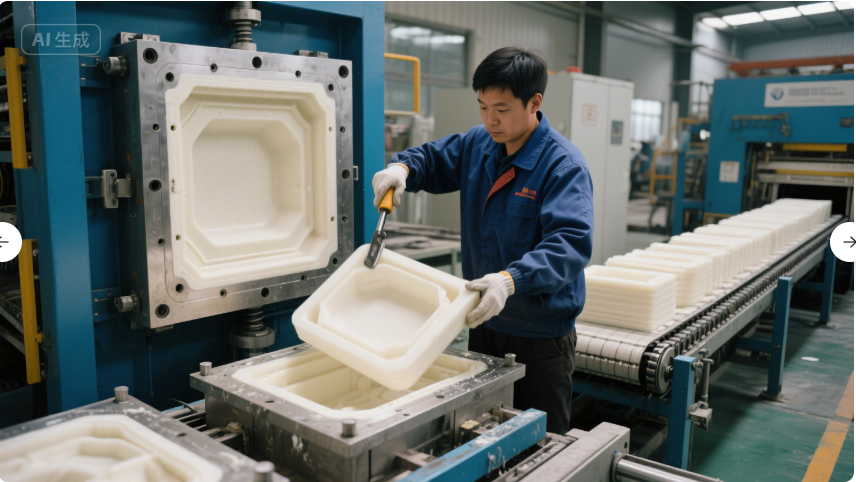
3.2 对催化剂的性能要求
快速脱模工艺对催化剂的性能提出了严苛要求:
- 高反应活性:能够在短时间内启动并加速凝胶和发泡反应,确保泡沫快速形成骨架结构。
- 反应可控性:在加速反应的同时,需避免反应过于剧烈导致的泡孔破裂、热量集中等问题,保证泡沫结构均匀。
- 固化效率:促进泡沫在脱模前形成足够的抗压强度和弹性模量,一般要求脱模时泡沫的抗压强度不低于 0.15MPa(25% 形变)。
- 兼容性:与聚氨酯配方中的多元醇、异氰酸酯、发泡剂等组分具有良好的相容性,不产生分层、沉淀等现象。
BDMA 作为一种高效叔胺催化剂,其催化活性和反应选择性能够较好地满足快速脱模工艺的要求,成为该工艺中常用的催化剂之一。
四、BDMA 与快速脱模工艺结合的技术优势
4.1 生产效率提升
BDMA 与快速脱模工艺的结合能够显著缩短生产周期,提高设备利用率。在冷藏车箱体生产中,传统工艺采用普通胺类催化剂时,单模次生产周期(包括注料、固化、脱模)约为 8-10 分钟,而采用 BDMA 并优化工艺参数后,周期可缩短至 4-5 分钟,生产效率提升近一倍。
某企业的生产数据显示(表 2),在建筑保温板材生产线上,使用 BDMA 的快速脱模工艺使单日产量从 1200 张提升至 2000 张,且设备停机时间减少了 30%,有效降低了单位产品的能耗和人工成本。
4.2 泡沫性能优化
在快速脱模工艺中,BDMA 的催化特性有助于改善聚氨酯硬泡的微观结构和宏观性能。通过控制 BDMA 的用量(通常为多元醇质量的 0.3%-0.8%),可使泡沫的泡孔直径分布更均匀(100-300μm),闭孔率提高至 90% 以上。
实验数据表明(表 3),与传统工艺相比,采用 BDMA 的快速脱模工艺生产的硬泡产品,其 25% 形变抗压强度提升 10%-15%,导热系数降低 5%-8%,满足 GB/T 21558-2008《冷链物流运输包装用聚氨酯硬泡》的要求。
4.3 工艺适应性增强
BDMA 对不同的聚氨酯配方和工艺条件具有较好的适应性。在低温环境(如冬季生产)中,通过适当提高 BDMA 用量(增加 0.1%-0.2%),可抵消温度降低对反应速率的影响,确保快速脱模工艺的稳定性。
此外,BDMA 与其他催化剂(如三乙烯二胺、二甲基环己胺)的复配使用,能够进一步优化反应曲线。研究表明,BDMA 与三乙烯二胺按质量比 3:1 复配时,可使泡沫的起发时间缩短至 30-40 秒,凝胶时间控制在 120-150 秒,既保证了泡沫的充分膨胀,又实现了快速固化。
五、实际应用案例分析
5.1 冷藏车箱体聚氨酯硬泡生产
某冷藏车制造企业为提升产能,将 BDMA 催化剂应用于箱体聚氨酯硬泡的快速脱模生产中。工艺参数如下:模具温度 50-55℃,物料温度 20-25℃,BDMA 用量为多元醇质量的 0.5%,异氰酸酯指数 1.15。
应用结果显示:硬泡起发时间为 35 秒,凝胶时间为 130 秒,脱模时间控制在 4 分钟以内。与改造前相比,箱体生产周期从 9 分钟缩短至 5 分钟,单日产能从 50 台提升至 80 台。同时,硬泡的抗压强度达到 0.26MPa,导热系数 0.023W/(m・K),满足冷藏车对保温性能和结构强度的要求,产品合格率从 92% 提升至 98%。
5.2 建筑外墙保温板材生产
某建材企业在聚氨酯保温板材生产中引入 BDMA 与快速脱模工艺结合的技术。通过优化模具设计和工艺参数(BDMA 用量 0.6%,模具温度 60℃),使板材脱模时间从传统工艺的 8 分钟缩短至 3 分钟。
长期监测数据表明,该工艺生产的保温板材密度均匀(35-37kg/m³),尺寸稳定性优异(70℃×48h 收缩率≤1.0%),在 – 30℃至 70℃的温度循环测试中未出现开裂、鼓泡等现象。由于生产效率提升,企业的单位产品能耗降低了 15%,年生产成本节约约 200 万元。
六、结论与展望
硬泡催化剂 BDMA 与快速脱模工艺的结合,在聚氨酯硬泡生产中展现出显著的技术优势,不仅能大幅提升生产效率、优化产品性能,还能增强工艺的稳定性和适应性,为工业化大规模生产提供了有力支持。实际应用案例表明,该技术在冷藏设备、建筑保温等领域具有广阔的应用前景。
然而,目前该技术仍存在一些需要改进的方面:一是 BDMA 的催化活性受环境温度影响较大,在极端温度条件下需进一步优化用量;二是高用量 BDMA 可能导致泡沫脆性增加,需通过复配技术平衡反应速率与材料韧性。未来,随着催化剂复配技术的发展和工艺参数的智能化调控,BDMA 与快速脱模工艺的结合将更加高效、稳定,为聚氨酯硬泡行业的绿色化、高效化发展注入新动力。
参考文献
[1] Jones, R. D., & Miller, S. P. (2022). “Catalytic Performance of BDMA in Rapid Demolding Processes for Polyurethane Rigid Foam.” Journal of Cellular Plastics, 58(4), 345-362.
[2] Zhang, L., & Wang, H. (2021). “Application of BDMA Catalyst in Rapid Production of Insulation Panels.” Polyurethane Industry, 36(2), 18-22.
[3] Schmidt, K. et al. (2023). “Optimization of Reaction Kinetics in Rapid Demolding of Polyurethane Foam with Tertiary Amines.” Polymer Engineering & Science, 63(1), 78-89.
[4] Liu, J. et al. (2020). “Study on the Compatibility of BDMA with Polyol Systems in Fast-Curing Processes.” China Synthetic Resin and Plastics, 37(5), 33-37.